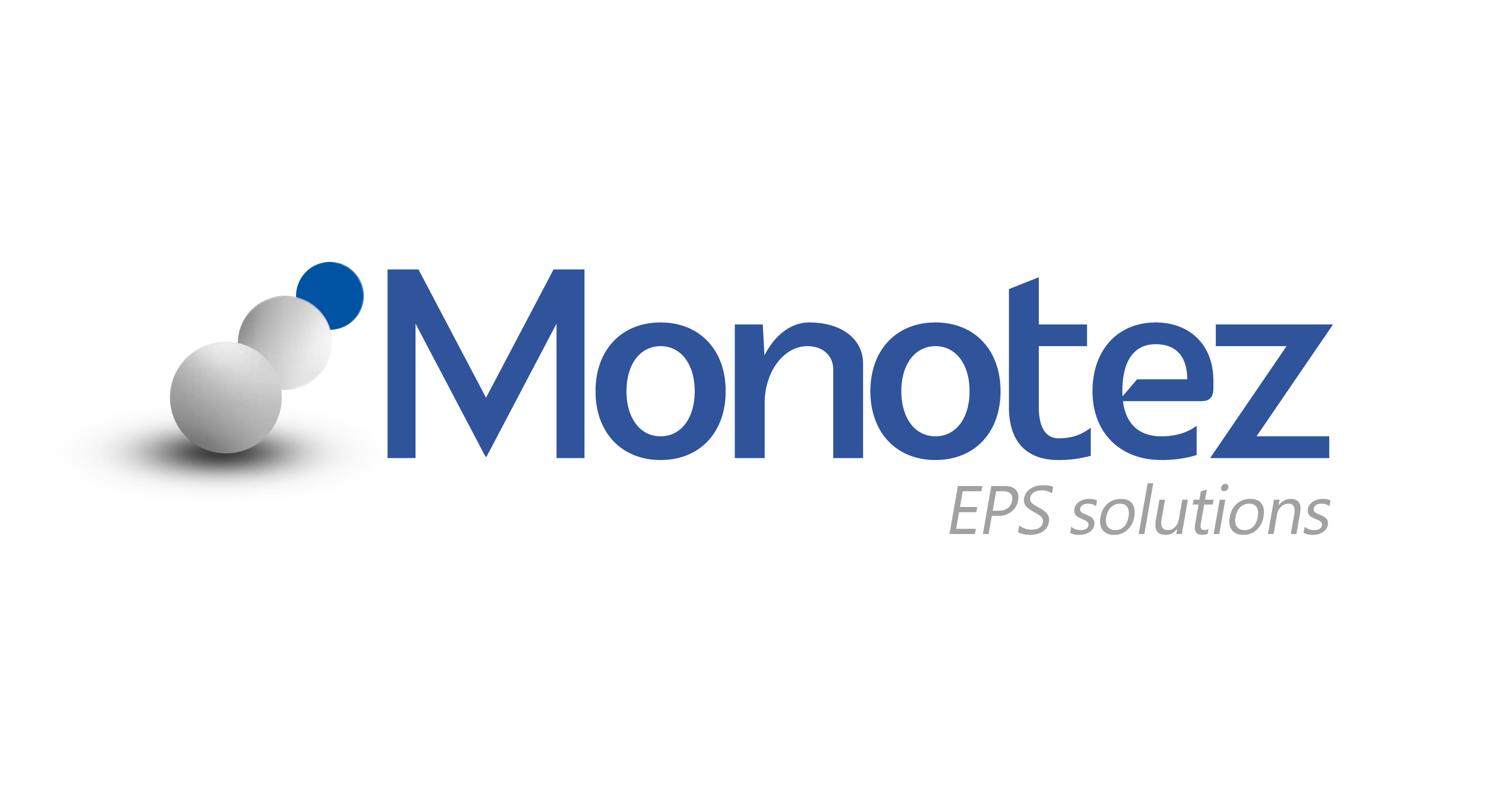
Monocell
Brand Information
Expandable Polystyrene (EPS)
High-Quality EPS under the Monocell® Trademark
Resinex distributes high-quality EPS (Expandable Polystyrene) produced by Monotez under the Monocell® trademark. The product range includes grades with flame retardant additives (FR grades) and without (R grades). Monocell® is supplied as a raw material that can be expanded and moulded into foam across a wide density range. It is ideal for producing boards or shape-moulded elements used in building thermal insulation, as well as packaging for the food industry and other specialised applications. Monocell® is available in various grades, allowing the selection of the appropriate bead size based on the final application and respective technology.
EPS Applications
Expandable Polystyrene is a thermoplastic material in spherical bead form, containing Pentane as a blowing agent, and is produced through the polymerisation of styrene monomer. The transformation process of EPS involves water vapour, causing the beads to expand up to 40 times their original volume within less than a minute.
Monocell® as Raw Material vs Expanded Polystyrene
Expanded Polystyrene (EPS) Production Process
The production of Expanded Polystyrene using Monocell® as raw material involves five phases:
- Pre-expansion: Each Polystyrene granule is expanded by exposure to steam, forming larger grains composed of closed cells.
- Conditioning: Post-expansion, the beads contain condensed vapour and small quantities of Pentane gas. After cooling, air partially replaces these components, gradually diffusing into the pores.
- Moulding: The beads are moulded into boards, blocks, or other shapes. The mould shapes the desired product and retains the pre-foam. Steam is used again to promote expansion and cause the fusion of each bead with its neighbours, forming a homogenous product.
- Shaping: After a short cooling period, the moulded block is removed from the machine and, following additional conditioning, can be cut into desired shapes using a hot wire element or other techniques.
- Post-production processing: The finished product can be laminated with other coverings such as foils, plastics, roof felts, fibre-board, or roof and wall cladding materials.
User Advantages
- Excellent Thermal Insulation: EPS consists of 98% air, making it an excellent thermal insulant.
- Proven Acoustic Insulator: It absorbs sound, both impact sound in floating floors and airborne sound for walls.
- Moisture Resistance: EPS is resistant to degradation by water.
- Lifetime Durability: EPS does not decompose, ensuring lifetime durability.
- Flexible Mechanical Features: The flexible production process makes EPS compatible with almost all applications.
- Versatility: EPS can be produced in almost any shape or size and is compatible with a wide range of materials.
- Cost-Effective: Compared to other insulation materials, EPS offers the best price/performance ratio.
- Easy Transportation: EPS is lightweight, ensuring fuel savings in transport.
- Easy to Install: EPS is lightweight, practical, safe, and easy to handle and install.
Monocell Products
Available In
Bulgaria, Romania, Slovenija, Portugal, France, Spain