Durability: The long polymer chains which constitute the plastics raw material make it extraordinarily difficult to break.
Safety: Plastics packaging is shatterproof and does not fragment into dangerous shards when dropped.
Hygiene: Plastics packaging is ideal for the packaging of foodstuffs, medicines and pharmaceuticals. It can be filled and sealed without human intervention. The materials used, both plastics raw materials and additives, fulfil all food safety legislation at national and European Union levels. Plastics products are customarily used as medical devices in intimate contact with body tissue and conform to the highest standards of safety in their life-saving uses.
Security: Plastics packaging can be produced and used with tamper-evident and child resistant closures. The transparency of the pack enables users to examine the condition of the goods prior to purchase.
Light Weight: Plastics packaging items are low in weight but high in strength. Hence products packed in plastics are easy to lift and handle by consumers and by personnel in the distribution chain.
Design Freedom: The properties of the materials combined with the array of processing technologies employed in the industry, ranging from injection and blow moulding to thermoforming, enable the production of an infinite number of pack shapes and configurations. Additionally the extensive range of colouring possibilities and the ease of printing and decoration facilitate brand identification and information for the consumer.
Related Products
Market Segments
Biaxially oriented film
Orientation of polymers enhances many of their properties, particularly the mechanical, impact, barrier and optical properties. Biaxial orientation has the added advantage of allowing this enhancement in two directions, avoiding any weakness in the transverse direction. Biaxial orientation is particularly important in films, where it allows the production of thinner films having superior mechanical, optical and barrier properties and, if required, the ability to shrink when reheated. For example, shrink and barrier properties are particularly important in meat packaging, whereas good mechanical and optical properties and no shrinkage are desired in box overwrap applications of confectionary and CDs.
Flat biaxial orientation is the most prevalent film orientation process. Most of the biaxially oriented polypropylene (BOPP) and polyester (BOPET) films used in packaging are produced using the technique detailed below. Very large units, capable of producing finished film over half a meter wide, are being installed around the world, bringing down processing costs per pound and creating plentiful supplies for the growing global flexible packaging market.
The Process: A unit commonly called a tenter frame line performs flat biaxial orientation. The term “tenter frame” refers to the CD orientation section. The process starts with a plasticating extruder feeding a first module that operates similarly to a cast film line.
With flat biaxial orientation, there are multiple chill and surface finishing rolls to handle the much thicker sheet that is formed. Orientation (or “stretching”) thins the polymer web proportionally to the orientation or stretch ratios. For example, to get to a 1-mil finished film with 5:1 stretch ratios in both MD and CD, the process must start out with roughly a 25-mil web of quenched polymer.
Once the extruded sheet has been quenched and its temperature stabilized, MD stretching is accomplished by pulling the sheet using rolls rotating with progressively increasing surface speeds; stretching takes place in small gaps between successive rollers. The small gaps minimize the potential for “neck in,” which is a reduction of the width of the web during the drawing or thinning processes.
Following MD stretching, endless chains with clips grasp the edges of the moving web and carry it into a multistage hot-air oven. The first oven stage is used to equilibrate the web at the desired temperature; this is followed by CD stretching, as the two tracks carrying the chains and clips are gradually moved farther apart, making the sheet wider. Further temperature conditioning in the final oven sections provides annealing or stress relaxation for dimensional stability and cools the film prior to winding.
Applications
- BOPP and BOPET - flexible packaging films - laminations (where they can be used in as-oriented form)
- BOPP and BOPET - flexible packaging films - vacuum-metallized (offering extra barrier protection)
- BOPP is widely used in salty, dry snack packaging
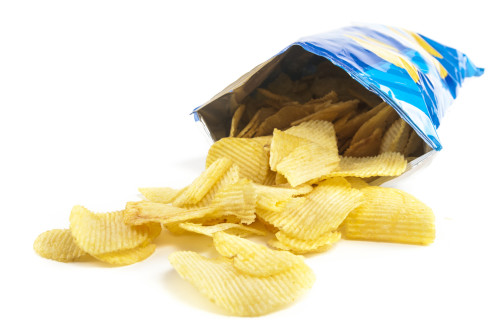
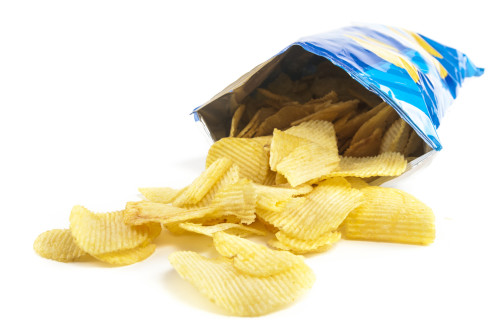
Biaxially oriented film
Orientation of polymers enhances many of their properties, particularly the mechanical, impact, barrier and optical properties. Biaxial orientation has the added advantage of allowing this enhancement in two directions, avoiding any weakness in the transverse direction. Biaxial orientation is particularly important in films, where it allows the production of thinner films having superior mechanical, optical and barrier properties and, if required, the ability to shrink when reheated. For example, shrink and barrier properties are particularly important in meat packaging, whereas good mechanical and optical properties and no shrinkage are desired in box overwrap applications of confectionary and CDs.
Flat biaxial orientation is the most prevalent film orientation process. Most of the biaxially oriented polypropylene (BOPP) and polyester (BOPET) films used in packaging are produced using the technique detailed below. Very large units, capable of producing finished film over half a meter wide, are being installed around the world, bringing down processing costs per pound and creating plentiful supplies for the growing global flexible packaging market.
The Process: A unit commonly called a tenter frame line performs flat biaxial orientation. The term “tenter frame” refers to the CD orientation section. The process starts with a plasticating extruder feeding a first module that operates similarly to a cast film line.
With flat biaxial orientation, there are multiple chill and surface finishing rolls to handle the much thicker sheet that is formed. Orientation (or “stretching”) thins the polymer web proportionally to the orientation or stretch ratios. For example, to get to a 1-mil finished film with 5:1 stretch ratios in both MD and CD, the process must start out with roughly a 25-mil web of quenched polymer.
Once the extruded sheet has been quenched and its temperature stabilized, MD stretching is accomplished by pulling the sheet using rolls rotating with progressively increasing surface speeds; stretching takes place in small gaps between successive rollers. The small gaps minimize the potential for “neck in,” which is a reduction of the width of the web during the drawing or thinning processes.
Following MD stretching, endless chains with clips grasp the edges of the moving web and carry it into a multistage hot-air oven. The first oven stage is used to equilibrate the web at the desired temperature; this is followed by CD stretching, as the two tracks carrying the chains and clips are gradually moved farther apart, making the sheet wider. Further temperature conditioning in the final oven sections provides annealing or stress relaxation for dimensional stability and cools the film prior to winding.
Applications
- BOPP and BOPET - flexible packaging films - laminations (where they can be used in as-oriented form)
- BOPP and BOPET - flexible packaging films - vacuum-metallized (offering extra barrier protection)
- BOPP is widely used in salty, dry snack packaging
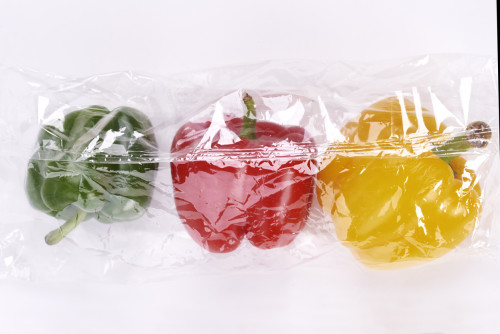
Food Packaging
Foodstuffs need to have packaging designed to offer a good barrier to oxygen in order to prolong the shelf life. Resinex has a range of materials offering flexibility, rigidity and good peel and seal properties that would benefit varying applications in the food packaging market. Transparency, taste and odour neural options are also key.
For frozen food films, tougher formulations are required. The frozen food packaging film industry is faced with keeping abreast of new consumer trends. Packaging materials must balance toughness, stiffness and mechanical resistance in order to enable increased packaging line speeds. In addition, the materials must allow for easy-opening without comprising good sealing qualities.
Further required properties include:
tougher film formulations for bigger packages;
barrier properties (water vapour/light barrier);
film down-gauging that retains an optimal balance between cost and resource reduction versus acceptable performance;
superior optical film properties and printability to support an increased focus on marketing and branding;
balanced surface friction for smooth processing on high speed Form Fill and Seal (FFS) equipment.
In processing films used for frozen food packaging, the films are normally extruded as a blend of Polyethylenes (PE) in either mono or co-extrusion. This allows film converters to tailor them precisely to the customer’s needs, whether these are performance-related (e.g. mechanical strength, cost, thickness or stiffness) or marketing-related (e.g. surface gloss, printing or stiffness).
Applications
- Food trays
- Films
- Pouches and casings
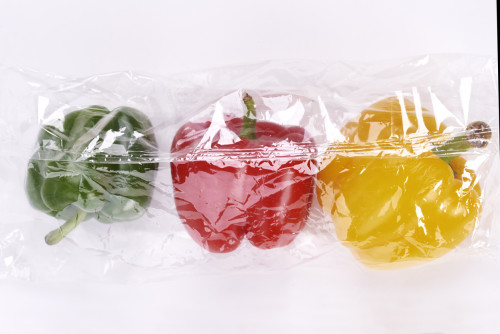
Food Packaging
Foodstuffs need to have packaging designed to offer a good barrier to oxygen in order to prolong the shelf life. Resinex has a range of materials offering flexibility, rigidity and good peel and seal properties that would benefit varying applications in the food packaging market. Transparency, taste and odour neural options are also key.
For frozen food films, tougher formulations are required. The frozen food packaging film industry is faced with keeping abreast of new consumer trends. Packaging materials must balance toughness, stiffness and mechanical resistance in order to enable increased packaging line speeds. In addition, the materials must allow for easy-opening without comprising good sealing qualities.
Further required properties include:
tougher film formulations for bigger packages;
barrier properties (water vapour/light barrier);
film down-gauging that retains an optimal balance between cost and resource reduction versus acceptable performance;
superior optical film properties and printability to support an increased focus on marketing and branding;
balanced surface friction for smooth processing on high speed Form Fill and Seal (FFS) equipment.
In processing films used for frozen food packaging, the films are normally extruded as a blend of Polyethylenes (PE) in either mono or co-extrusion. This allows film converters to tailor them precisely to the customer’s needs, whether these are performance-related (e.g. mechanical strength, cost, thickness or stiffness) or marketing-related (e.g. surface gloss, printing or stiffness).
Applications
- Food trays
- Films
- Pouches and casings
General
Plastics packaging prevents food waste. The durability and sealability of plastics packaging protects goods from deterioration and increases shelf life. With modified atmosphere packaging made from plastics, shelf life can be increased from 5 to 10 days, allowing food loss in stores to be reduced from 16% to 4%.
Traditionally grapes were sold in loose bunches. Grapes are now sold in sealed trays so that the loose ones stay with the bunch. This has reduced waste in stores typically by over 20%
Applications
- Metal free twists and ties
- Coatings
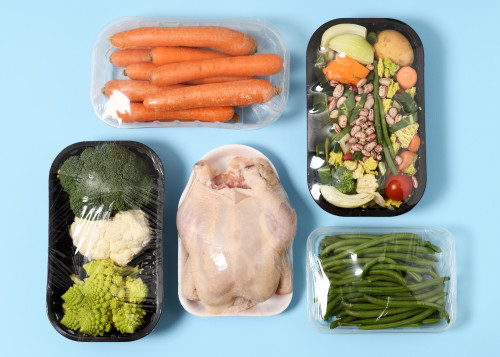
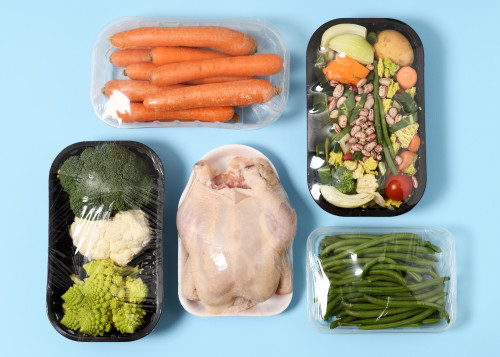
General
Plastics packaging prevents food waste. The durability and sealability of plastics packaging protects goods from deterioration and increases shelf life. With modified atmosphere packaging made from plastics, shelf life can be increased from 5 to 10 days, allowing food loss in stores to be reduced from 16% to 4%.
Traditionally grapes were sold in loose bunches. Grapes are now sold in sealed trays so that the loose ones stay with the bunch. This has reduced waste in stores typically by over 20%
Applications
- Metal free twists and ties
- Coatings
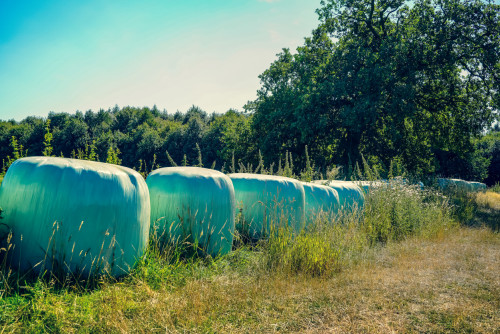
Heavy duty packaging
As part of a multi layer structure or a single polymer, the applications in this segment need to be durable and puncture resistant to ensure no material loss. Anti static and with good tear strength, we have a broad portfolio of materials.
Applications
- PE liner
- Stretch hood layer
- Shipping sacks
- Protective packaging
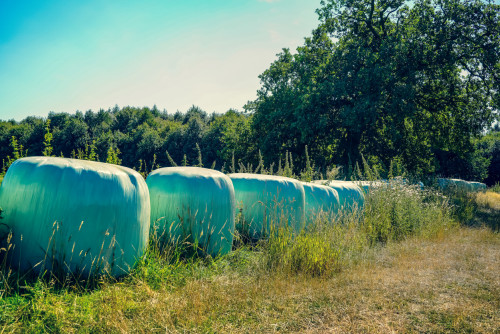
Heavy duty packaging
As part of a multi layer structure or a single polymer, the applications in this segment need to be durable and puncture resistant to ensure no material loss. Anti static and with good tear strength, we have a broad portfolio of materials.
Applications
- PE liner
- Stretch hood layer
- Shipping sacks
- Protective packaging
Labels
A good surface finish with good clarity is needed to enable a clear view of the label details in some cases. With extrusion profiles there are a range of possibilities in our portfolio. Other applications require uv protection and chemical resistance as well as being laser markable. We have a range of polymers to suit your needs.
Dow™ also offers material for film labels which require excellent optics and high stiffness for thin gauge films.
Applications
- Price profiles
- Animal ear tags
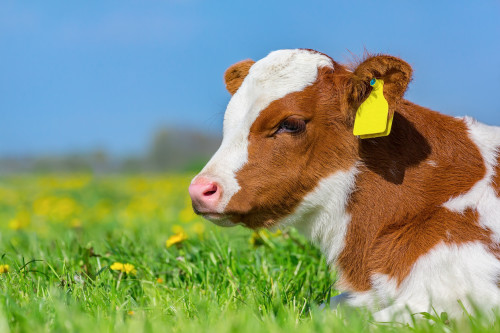
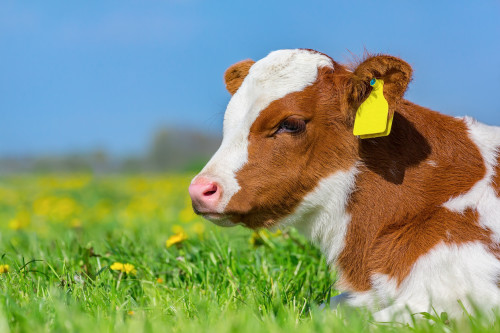
Labels
A good surface finish with good clarity is needed to enable a clear view of the label details in some cases. With extrusion profiles there are a range of possibilities in our portfolio. Other applications require uv protection and chemical resistance as well as being laser markable. We have a range of polymers to suit your needs.
Dow™ also offers material for film labels which require excellent optics and high stiffness for thin gauge films.
Applications
- Price profiles
- Animal ear tags
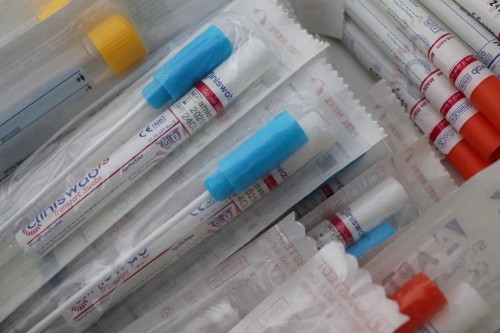
Medical
Resinex provides technical expertise in order to choose the correct material for your application. With the necessary certification for biocompatibility or EU Pharmacopoiea, we are here to offer solutions. From Dow™ Health Plus, Trinseo Styron MED. Exxon PP to Celanese Ateva, we have the cooperation of reliable suppliers to offer trusted materials.
Applications
- Pharmaceutical bags and seals
- Medicine cup, caps and closures
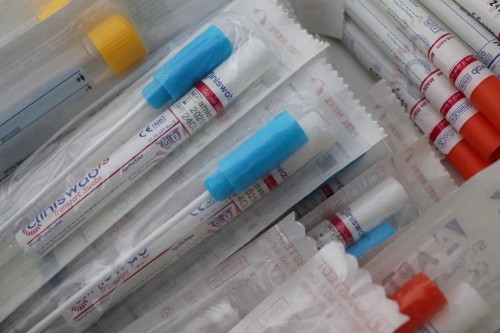
Medical
Resinex provides technical expertise in order to choose the correct material for your application. With the necessary certification for biocompatibility or EU Pharmacopoiea, we are here to offer solutions. From Dow™ Health Plus, Trinseo Styron MED. Exxon PP to Celanese Ateva, we have the cooperation of reliable suppliers to offer trusted materials.
Applications
- Pharmaceutical bags and seals
- Medicine cup, caps and closures
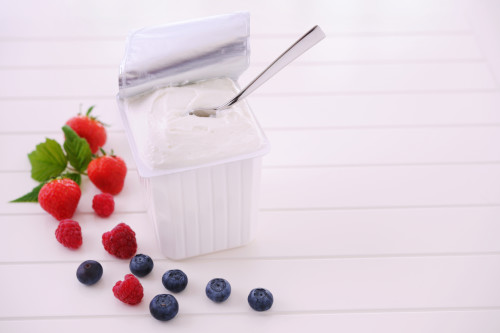
Seal/peel
Seal and peel films are used predominantly in the food industry, offering flexibility of design but preserving the integrity of the foodstuffs. Or protecting medical components, consumer products and more.
Our supply partner, Dow™ are offering single pellet solutions for ease of use:
Peel consistency over time for more reliability
Individual polymer solutions offering higher versatility
Optimized formulations that provide an excellent combination of:
» Low Heat Seal Initiation Temperature (HSIT) for packaging speed
» Broad Hot Tack & Heat Seal Window for pack integrity
» Reliable targeted Peel-Strength
» Compatibility with variety of Substrates and Production Processes
» Transparency Set by Package Type
» No tear strings when opened
Applications
- Sealing used in tubing
- Food packaging
- Consumer products
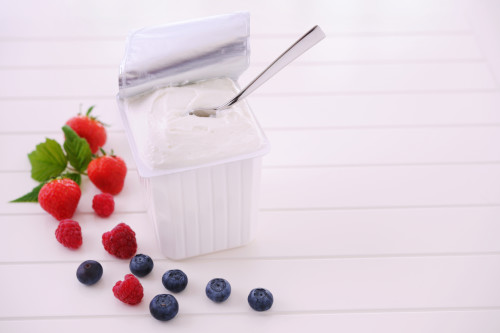
Seal/peel
Seal and peel films are used predominantly in the food industry, offering flexibility of design but preserving the integrity of the foodstuffs. Or protecting medical components, consumer products and more.
Our supply partner, Dow™ are offering single pellet solutions for ease of use:
Peel consistency over time for more reliability
Individual polymer solutions offering higher versatility
Optimized formulations that provide an excellent combination of:
» Low Heat Seal Initiation Temperature (HSIT) for packaging speed
» Broad Hot Tack & Heat Seal Window for pack integrity
» Reliable targeted Peel-Strength
» Compatibility with variety of Substrates and Production Processes
» Transparency Set by Package Type
» No tear strings when opened
Applications
- Sealing used in tubing
- Food packaging
- Consumer products
Shrink film
On exposure to heat, the film shrinks to pack tightly around the product providing a protective layer and keeping items in place. Usually made using polyethylene, properties include clarity, good tear strength and toughness.
Applications
- Biaxially oriented PE (BOPE) film
- Blown film
- Shrink film


Shrink film
On exposure to heat, the film shrinks to pack tightly around the product providing a protective layer and keeping items in place. Usually made using polyethylene, properties include clarity, good tear strength and toughness.
Applications
- Biaxially oriented PE (BOPE) film
- Blown film
- Shrink film